Belgisch familiebedrijf stunt met eerste CO2-negatieve gevelsteen!
Baksteenproducenten hebben niet zo gigantisch veel pistes om hun producten te verduurzamen. Dat was althans de gangbare gedachte... tot Vandersanden Group onlangs vriend en vijand verraste met de aankondiging van de ‘Pirrouet’. Door een uniek en energieloos fabricatieproces te combineren met gerecycleerde grondstoffen zou dit immers de eerste CO2-negatieve gevelsteen ter wereld zijn. Bovendien openen er zich ook nieuwe architecturale deuren omdat deze innovatie een verscheidenheid aan vormen en kleuren kan worden gemaakt.
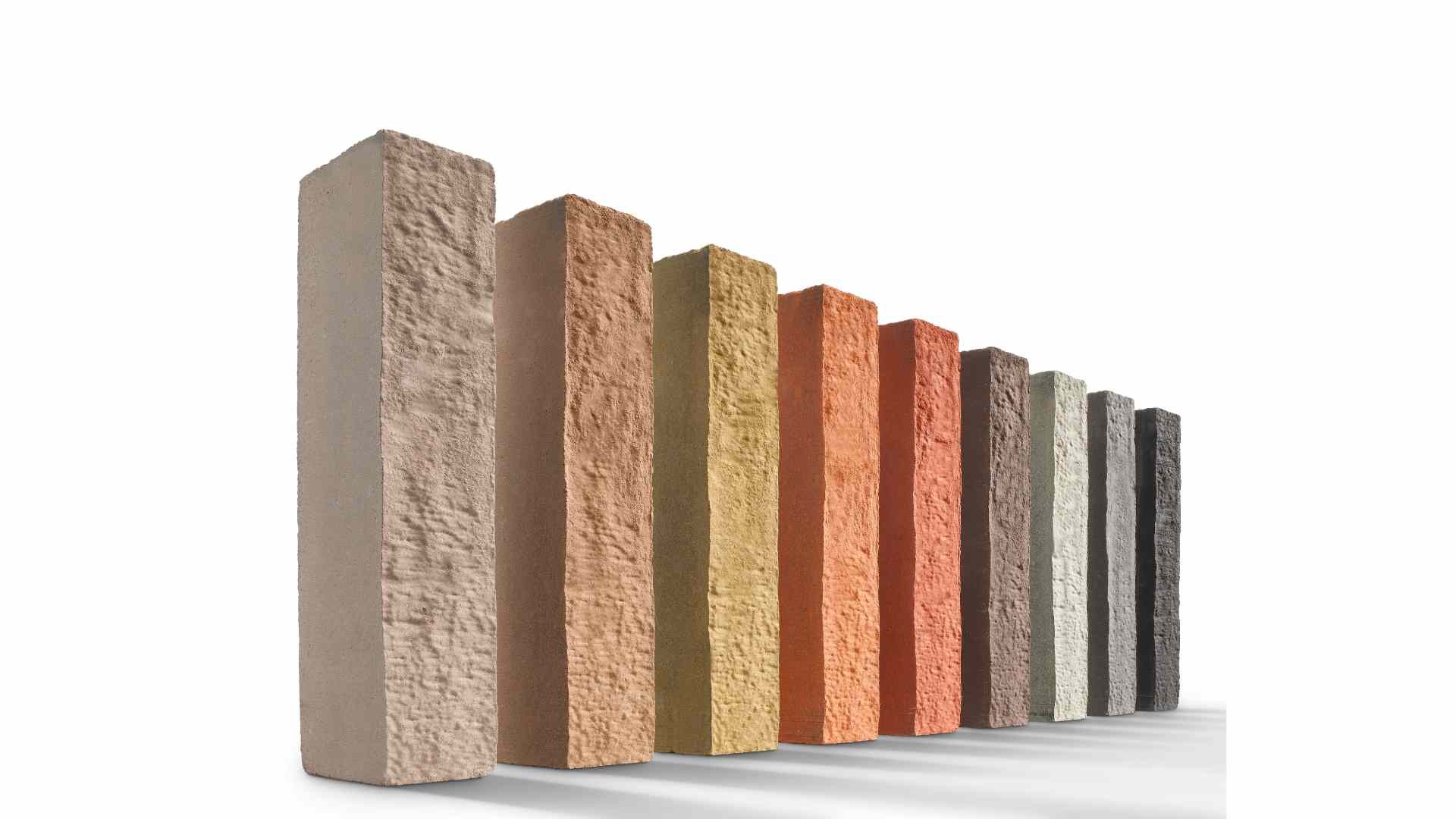
De duurzaamheidsgedachte zet de Europese baksteenproducenten al meerdere jaren flink onder druk. Ook Vandersanden Group zoekt al lange tijd naar manieren om met deze uitdaging om te springen. “Net als veel andere industriële bedrijven proberen we onze ecologische voetafdruk te reduceren door te investeren in PV-panelen, windmolens en elektrische wagens”, vertelt ceo Rudi Peeters. “Dit zijn pistes die producten zelf niet substantieel verduurzamen. Baksteenproducenten kunnen op ecologisch vlak pas echt het verschil maken door het productieproces energiezuiniger te maken en op natuurlijke grondstoffen te besparen. Daarom zoekt onze R&D al tien jaar naar manieren om deze ambities te verwezenlijken. Helaas stootten we op dezelfde barrière als onze concullega’s: de oplossingen liggen niet voor de hand. Tot het geluk ons in 2017 een handje toestak.”
Toevallige ontdekking
Het geluk nam de gedaante aan van Orbix, een ‘zero waste’ bedrijf uit Genk dat zich toelegt op de ontwikkeling en verkoop van duurzame materialen en technologieën voor de bouw- en staalsector. “Bij het recupereren van RVS uit staalslakken had deze onderneming per toeval ontdekt dat de reststroom aan de lucht uithardt tot een hard product dat de baksteen benadert,” vertelt Bert Neyens, R&D-manager van Vandersanden Group. “Met het oog op de commercialisering van deze fractie klopte Orbix bij ons aan. Natuurlijk waren we meteen geïnteresseerd, want een energieloos productieproces waarbij CO2 zich met de steen verbindt - in plaats van CO2 uit te stoten - is natuurlijk dé manier bij uitstek om onze sector te verduurzamen. Dat er ook nog eens reststromen als grondstof konden worden ingezet, maakte het verhaal dubbel zo interessant.”
“Via certificeringsinstituten willen we ervoor zorgen dat de duurzaamheidswaarde van de ‘Pirrouet’ objectief wordt vastgelegd.”
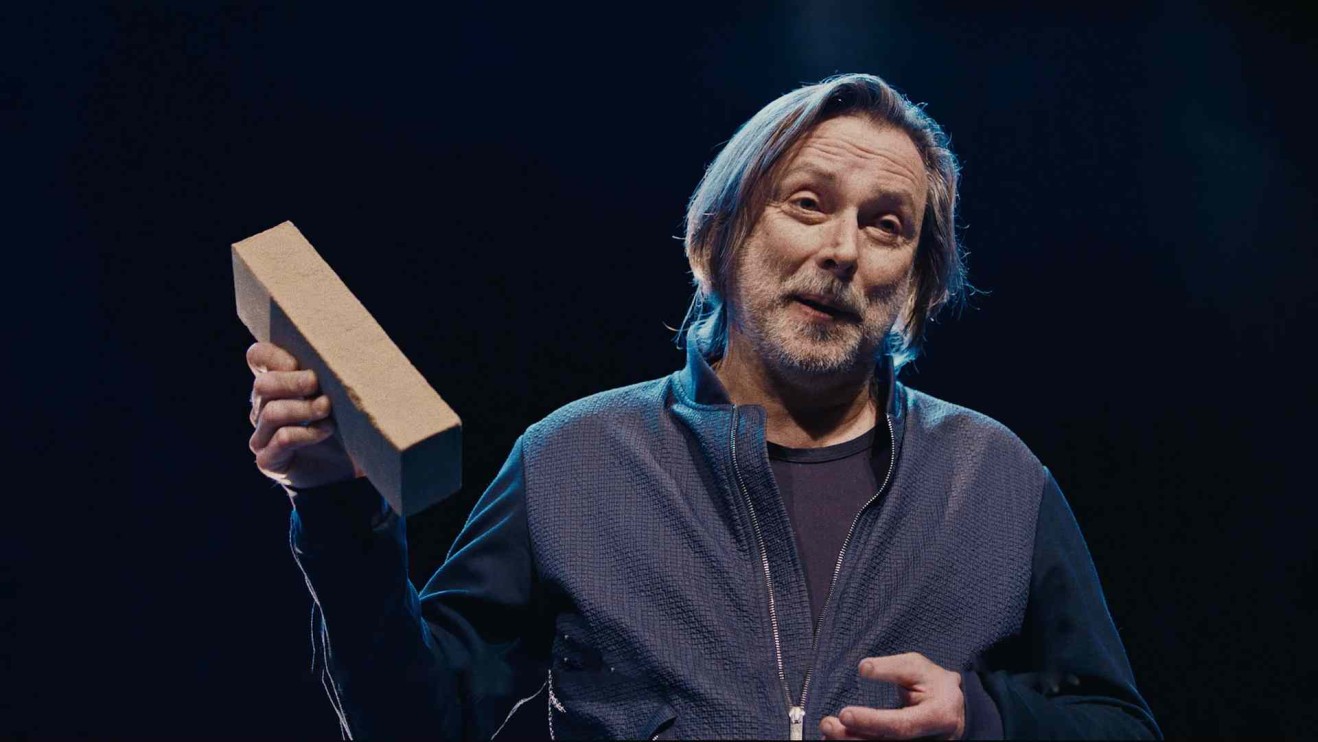
Door middel van carbonatatie
Het idee was mooi, maar de praktijk was een ander paar mouwen. Niet alleen moest een manier worden gevonden om het uithardingsproces te versnellen. Ook diende de ideale mix van grondstoffen te worden geformuleerd om een gevelsteen te maken die qua karakteristieken en ‘look & feel’ met het traditionele aanbod vergelijkbaar is. “Een extra voorwaarde was dat de prijs voor de klant onveranderd bleef”, aldus Rudi Peeters. “Daarnaast wilden we dat de rest van het proces CO2-neutraal bleef.” Uiteindelijk ging Orbix samen met Vito aan de slag om het uithardingsproces te versnellen en te industrialiseren. Het resultaat werd ‘carbonatatie’ gedoopt en door de initiatiefnemer gepatenteerd. “Wij kregen een licentie om het proces toe te passen bij de realisatie van de Pirrouet”, legt Rudi Peeters uit. “Concreet maakt carbonatatie gebruik van CO2 uit andere fabrieken. Deze wordt in liquide toestand getransporteerd naar onze productiefaciliteit waar ze in gasvorm wordt toegediend in een klimaatkamer. Daar gaat de CO2 een permanente verbinding aan met de calciumhoudende grondstoffen, namelijk de minerale metaalslakken en zand. Hierdoor ontstaan carbonaten: een harde kalksteenachtige steen die aan de Europese norm voor keramische gevelstenen voldoet.”
Van baksteen naar gevelsteen
In een eerste denkfase wilde Vandersanden het recyclaat toepassen als alternatieve grondstof voor de productie van keramische baksteen. Dit idee werd uiteindelijk afgevoerd omdat het bakproces een zekere kleureninstabiliteit veroorzaakte. Toen de carbonatatie-technologie op punt stond, evolueerde het onderzoek van de R&D naar het ontwikkelen van een totaal nieuwe gevelsteen die fysisch en esthetisch het traditionele alternatief benadert. “Bovendien is dit product grotendeels circulair,” vertelt Bert Neyens. “De ‘Pirrouet’ bestaat tot 80% uit de minerale reststromen carbinox en stinox uit de staalindustrie. We gebruiken dus slechts 20% primaire grondstoffen, zoals zand, water en eventuele kleurstoffen. In de toekomst beogen we om dit percentage nog verder te reduceren door andere reststromen aan te wenden.”
Negatieve CO2-score
Het productieproces is vrij eenvoudig: de reststromen worden in een grote mixer met zand en water vermengd. Vervolgens worden de stenen in een mal geperst, een proces waarbij ook kleurpigment wordt toegevoegd. “Het persen gebeurt hydraulisch met energie die door onze eigen pv-panelen en windmolen worden gegenereerd”, aldus Rudi Peeters. De laatste stap is het uitdrogen met CO2 gedurende 24 à 30 uur in een klimaatkamer (gelijkaardig aan een droogkamer in een traditioneel productieproces). “Tijdens dit proces wordt per ton stenen 60 kg CO2 opgenomen. Dit verbindt zich permanent met de aanwezige calciumhydroxide”, vervolgt Rudi Peeters. “In feite is dat ook een afvalstroom. In plaats dat ze in de atmosfeer terechtkomt, wordt ze nu door ons gerecycleerd, wat uiteraard nog veel ecologischer is dan ze ondergronds in lege aardgasvelden op te slaan.” Bert Neyens vervolgt: “Het resultaat is een gevelsteen die qua ecologische voetafdruk beter scoort dan eender welke andere gevelsteen ter wereld: we halen immers een negatieve CO2-score!”
In het eerste trimester van 2024 zal de productie opstarten, aanvankelijk met een capaciteit van twintig miljoen stenen per jaar.
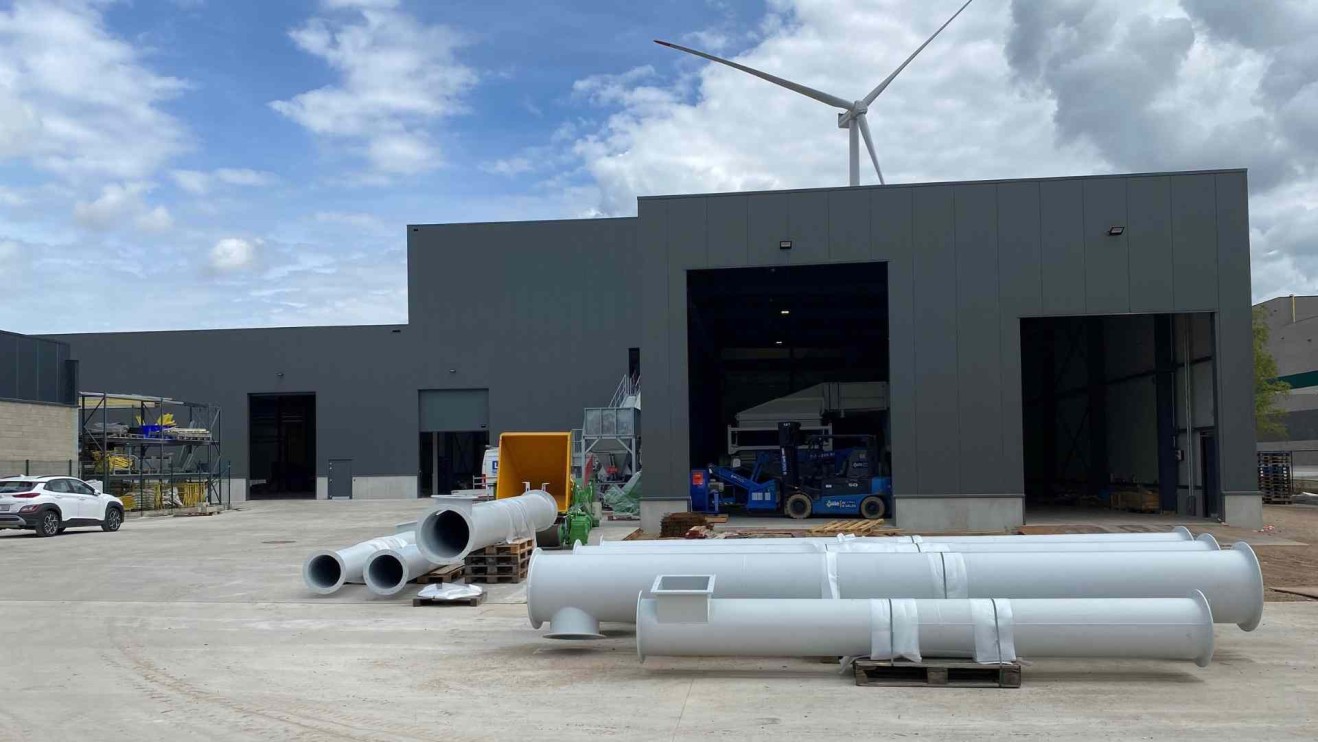
Brede waaier aan mogelijkheden
Vandersanden Group is vandaag bezig met de bouw van een gloednieuwe ‘Pirrouet’-fabriek in Lanklaar. In het eerste trimester van 2024 zal de productie opstarten, aanvankelijk met een capaciteit van twintig miljoen stenen per jaar. “In een eerste fase zullen we de nieuwe gevelsteen in negen kleuren en twee verschillende vormen op de markt brengen, met de esthetische ‘look & feel’ van een baksteen’,” aldus Bert Neyens. “Hiermee benutten we echter maar een fractie van de mogelijkheden dat het productieproces biedt. Omdat we de stenen in een mal persen, kunnen we op termijn een wijde range van vormen aanbieden. Ook laat het proces toe om de textuur te variëren van uiterst glad, over zwaar reliëf, tot decoratieve prints. Tenslotte kunnen de meest uiteenlopende kleuren worden toegepast. Het hoeft geen betoog dat architecten dit graag horen…”
Grootse plannen
De nieuwe Living Tomorrow-toren is alvast een mooi visitekaartje van de Pirrouet. Daar werden de drie onderste lagen met de prismavormige variant in azuurblauw afgewerkt. “Natuurlijk is er wel een zekere kwantiteit nodig om dit soort van maatwerk betaalbaar te houden”, aldus Rudi Peeters. “Toch is dat maar een kleine horde om te nemen. Nog voor onze innovatie op de markt is, hebben we al meerdere bestellingen ontvangen. Daarom is het best mogelijk dat we de resterende capaciteit in Lanklaar – eveneens twintig miljoen stenen per jaar – benutten voor de productie van maatwerk. Of we maken strips als tweede grote productgroep. De toekomst zal moeten uitwijzen waar zich de grootste vraag stelt. We willen trouwens op relatief korte termijn extra fabrieken bouwen, in België of onze buurlanden. Liefst op sites van bedrijven die intensief energie produceren, zodat we deze CO2 voor ons productieproces kunnen inzetten en daarmee de ecologische voetafdruk verder reduceren. Tevens willen we het patent op de gevelsteen commercialiseren zodat ook concullega’s de weg van CO2-negatieve productie kunnen inslaan.”
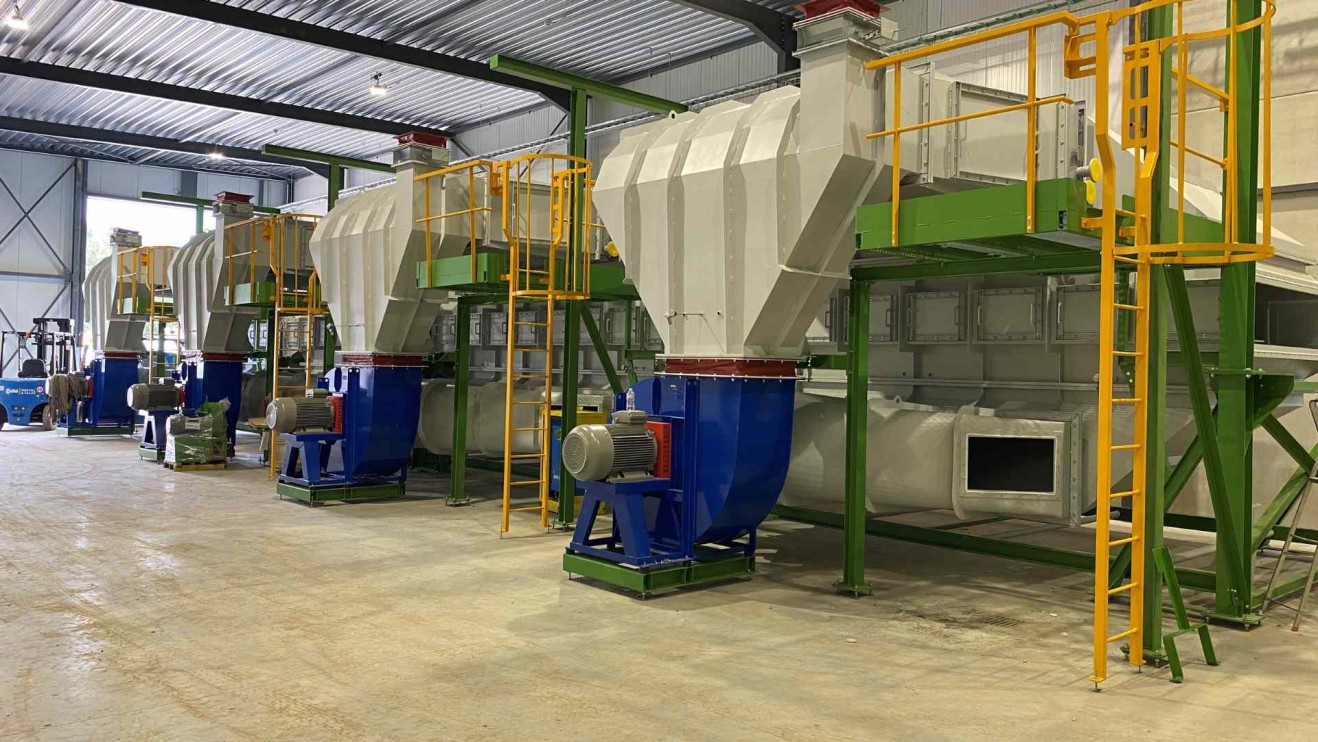
Op naar droogstapeltechnieken?
Vraag is natuurlijk welke impact dergelijke gevelstenen op de processen van de aannemers zullen hebben. Vandersanden Group is resoluut in het antwoord: “geen, want de ‘Pirrouet’ kan op eenzelfde manier worden verwerkt als een traditionele gevelsteen, dus zowel met gewone mortel als lijm.” Bert Neyens: “Deze nieuwe productlijn is dermate maatvast dat er minimale voegen van 1 à 2 mm kunnen worden gerealiseerd. Daarom experimenteren we nu ook met droogstapeltechnieken. Concreet werken we aan een kliksysteem dat een maximale vormvastheid vereist. Bij normale gevelstenen kan dit niet worden toegepast omdat deze allemaal minimale verschillen in vorm en afmeting vertonen, én bovendien ook krimpen of uitzetten naargelang de weersomstandigheden. Met de ‘Pirrouet’ zijn deze problemen van de baan, waardoor de weg vrij is gemaakt voor een realistisch scenario van bouwen zonder mortel of lijm. Trouwens, de kans is groot dat de vormvastheid van onze nieuwe gevelsteen de introductie van (metsel)robots zal versnellen. Elke afwijking in traditionele bakstenen of strips vereisen immers een complex ‘denkproces’ van de robot, wat momenteel vaak nog een brug te ver is voor een rendabele toepassing van dit soort automatisering.” Rudi Peeters vervolgt: “Last but not least willen we uittesten of we nog andere reststromen of recuperatiesystemen kunnen aanwenden. Ook willen we via certificeringsinstituten ervoor zorgen dat de duurzaamheidswaarde objectief wordt vastgelegd. We zijn er immers van overtuigd dat de wetgever steeds strengere verplichtingen zal opleggen. Daar willen we proactief op inspelen door de ‘Pirrouet’ van de nodige certificaten en geverifieerde duurzaamheidswaarden te voorzien.”
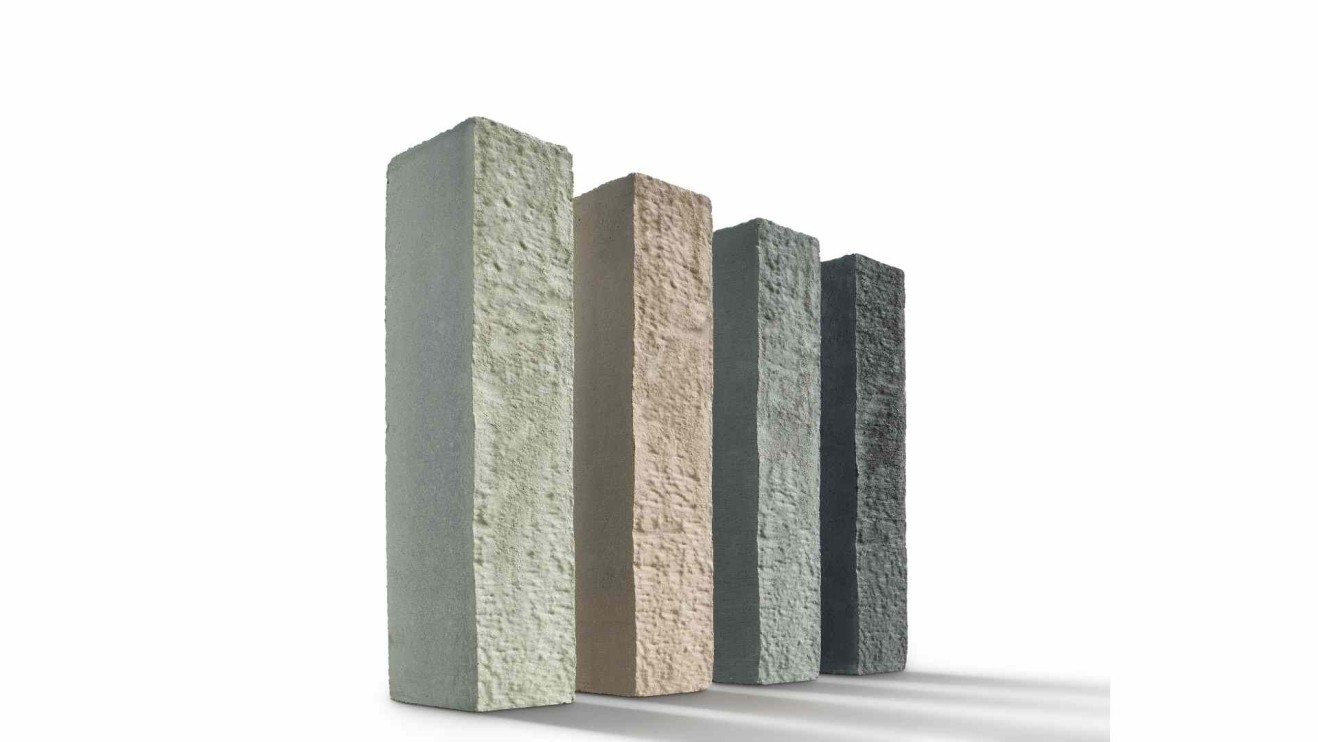
De naam Pirrouet
De naam werd niet in het wilde weg gekozen. Het is een eerbetoon aan de voormalige ceo Pirre Wuytack. “Hij was een visionair man die de grondlegger en aanjager is geweest van deze baanbrekende duurzame innovatie”, vertelt Rudi Peeters. “Verder verwijst de naam naar de 360°-rotatie, het circulaire en de beweging naar een CO2-neutrale wereld.”
De Living Tomorrow toren demonstreert mooi de kleur- en vormmogelijkheden van de ‘Pirrouet’.
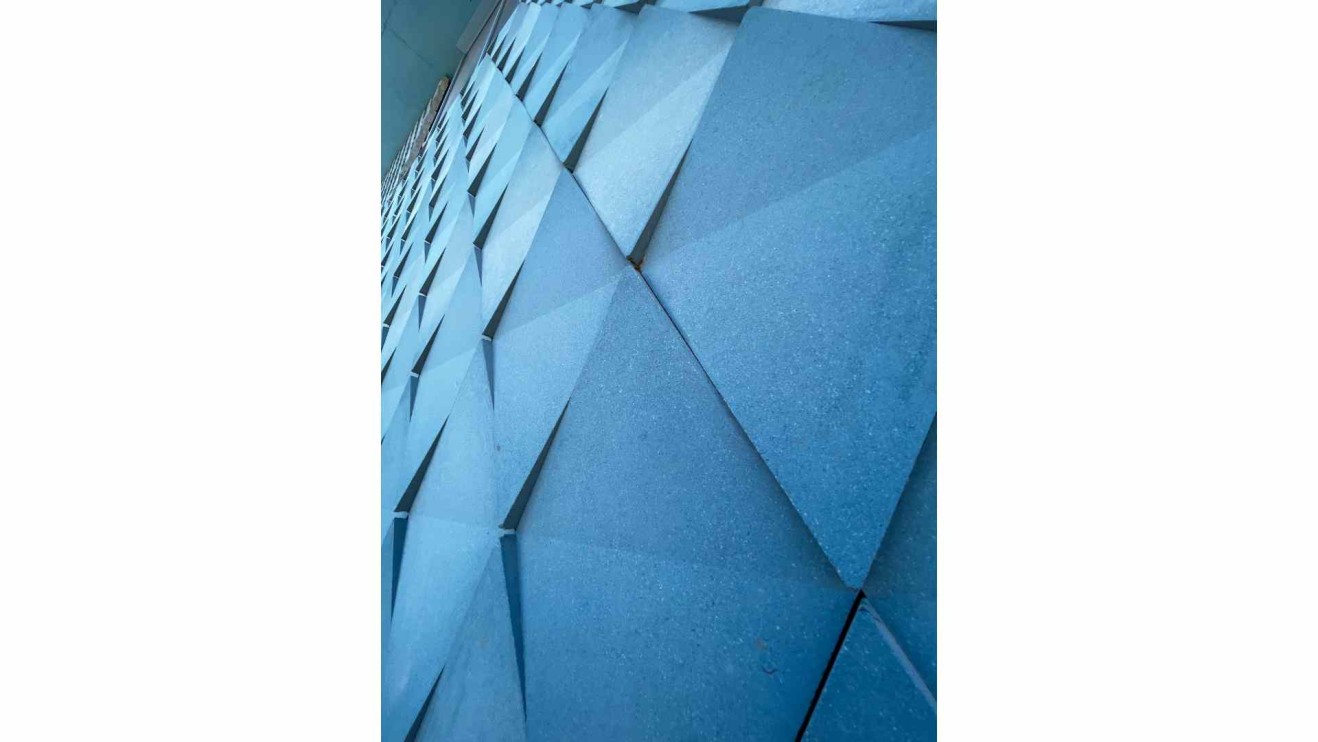
De nieuwe Living Tomorrow-toren is alvast een mooi visitekaartje: daar werden de drie onderste lagen met de prismavormige variant in azuurblauw afgewerkt.
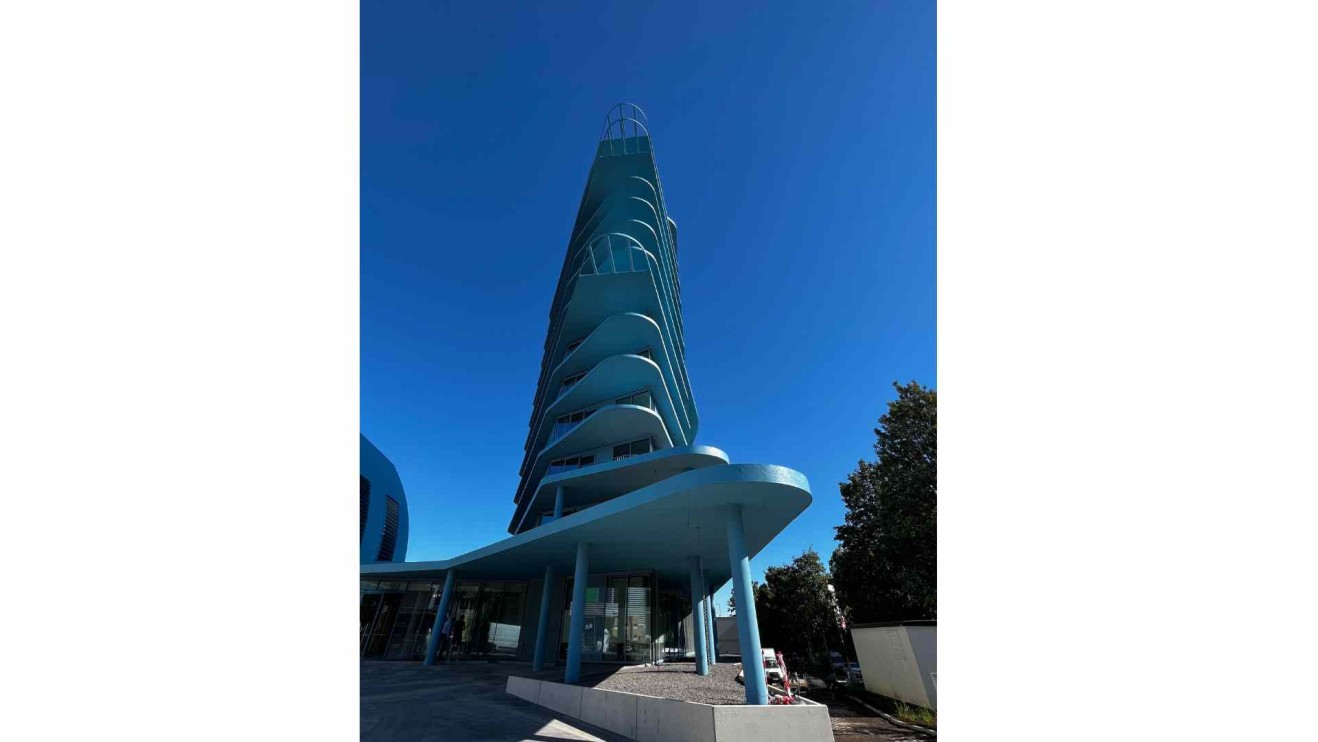