Isoleren met gras? Duurzamer kan het niet!
Na twee valse starts is Gramitherm nu toch volop bezig met de markt van biobased isolatiematerialen te veroveren. Het gaat snel, en dat is niet zo verbazingwekkend. Deze Waalse firma fabriceert immers een product dat qua minimale ecologische voetafdruk alle andere alternatieven van de mat veegt. De isolatieplaten bestaan namelijk uit grasvezel in combinatie met gerecycleerde jute. Samen met biomethanisatie en een lokale aanvoer van de grondstof zou het volgens de initiatiefnemers een van de meest duurzame isolatieoplossingen ter wereld zijn.
Vorig jaar produceerde Gramitherm 15.000 m³ panelen die via verdelers en groothandelaars in België, Nederland, Frankrijk, Luxemburg en Italië in de markt werden gezet.
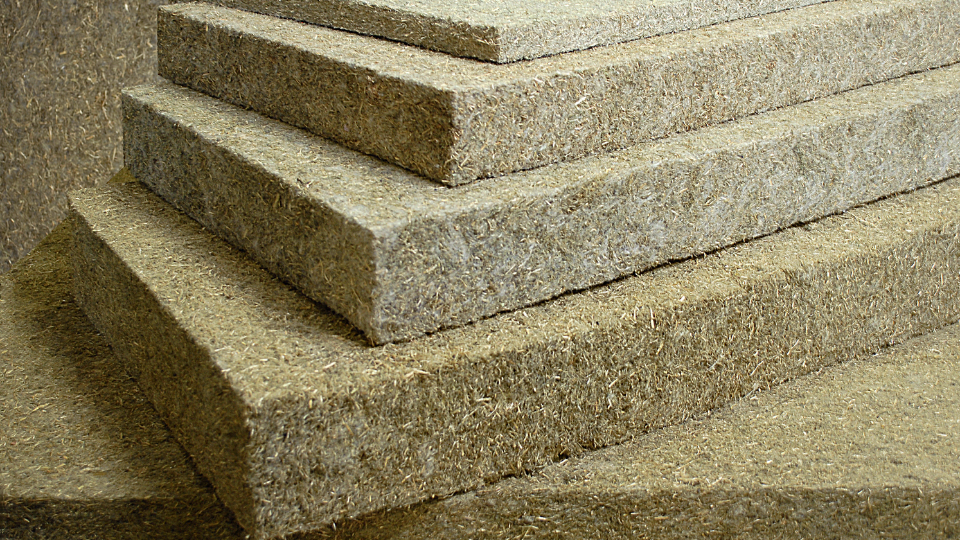
Alles begon met een Zwitserse onderzoeker aan de Ecole
Polytechnique de Lausanne die de mogelijkheden van gras als ecologische
grondstof onderzocht. Stefan Grass (what’s in a name?) slaagde erin om een
proces te ontwikkelen dat toelaat de grasvezel af te scheiden. “Hij probeerde
zelf het concept te commercialiseren, maar bedrijfsbeheer, verkoop en marketing
waren niet echt zijn ding,” vertelt Florent Timmermans, mede-zaakvoerder van
Gramitherm. “Uiteindelijk besloot hij om een overnemer te zoeken. Zo kwam hij
bij Christian Roggeman terecht, een Belg die bij Owens Corning werkte en graag
het pad van het zelfstandige ondernemerschap wou inslaan. Aanvankelijk startte
Christian in Oostenrijk een eigen fabriekje op om grasvezel te produceren. Deze
werden dan door een derde partij in isolatieplaten verwerkt, maar die werd al
snel door grote groep overgenomen die geen graten in de grasisolatie zag.
Christian, die wel sterk in het concept geloofde, besloot de volledige
activiteit naar België over te hevelen. En zo is hij in 2019 in de oude
vestigingen van Saint-Gobain in Auvelais met Gramitherm gestart.”
Het gras wordt geperst, waarna de grasvezel wordt gedroogd om als grondstof voor de panelen te gebruiken.
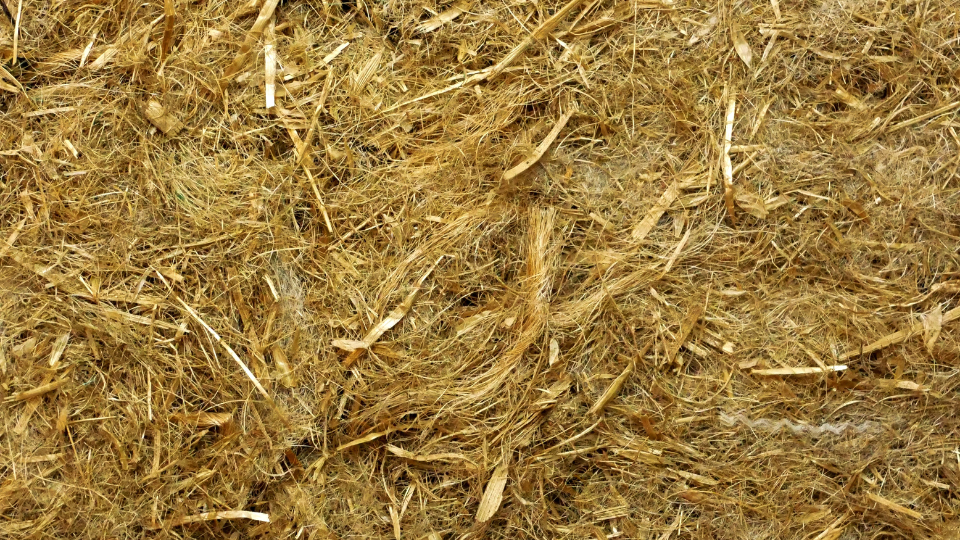
Op twee locaties
Weliswaar werd het concept van Oostenrijk niet klakkeloos gekopieerd. Christian Roggeman ontwikkelde een gloednieuw productieproces dat zich op twee locaties afspeelt om de ecologische voetafdruk te minimaliseren. “Twee sites: het lijkt een contradictio in terminis, maar dat is het zeker niet,” aldus Florent Timmermans. “We maken de grasvezel op het terrein van een biomethanisatiefaciliteit in Nijvel omdat dit enerzijds toelaat het sap dat uit het gras wordt geperst meteen in energie om te zetten, en anderzijds de warmte van het biomethanisatieproces te gebruiken om de grasvezel te drogen. Dit laatste is nu eenmaal de meest energieverslindende stap van ons proces. Vandaar dat het toch wel enige tijd heeft geduurd vooraleer we de juiste manier vonden om grasvezels op een kwalitatieve, duurzame en kostenefficiënte manier te produceren. Dat deze locatie meteen ook alle vergunning heeft om biomassa te verwerken, is dan weer een economisch en administratief voordeel voor een startup als Gramitherm. De effectieve productie van de isolatieplaten gebeurt in Auvelais waar we intussen een quasi volautomatische en energiezuinige lijn hebben uitgebouwd. We blijven trouwens sleutelen aan dit proces. Zo zijn we nu bezig met een project om de warmte van de oven te recupereren zodat we ook gras in Auvelais kunnen drogen. Daarnaast experimenteren we met de ontwikkeling van nieuwe producten, zoals akoestische en ‘high density’ isolatie. Bovendien zijn we nu eveneens in staat om op aanvraag isolatieplaten van andere biobased materialen te maken.”
De technische eigenschappen van grasisolatie zijn vergelijkbaar met deze van houtpanelen.
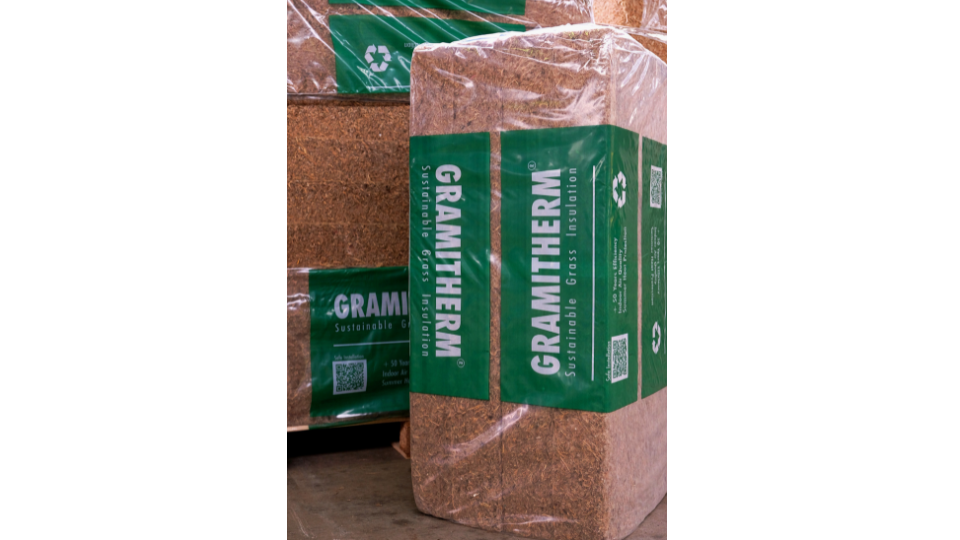
Meest duurzame grondstof
De corebusiness van Gramitherm blijft echter de productie van isolatieplaten op basis van grasvezel. “Onze grondstof wordt vandaag geleverd door twee grote bedrijven die het groenonderhoud doen aan kanalen en rivieren, de middenberm van autosnelwegen, (natuur)parken, diverse gemeentes…” legt Florent Timmermans uit. “Het gras dat op deze locaties wordt gemaaid, mag niet voor dierenvoeder worden gebruikt vanwege het risico op contaminaties. Ook mag het niet blijven liggen omdat het gras dan nog sneller groeit en er bodemonstabiliteit kan ontstaan. Als resultaat verrotten jaarlijks tonnen en tonnen gemaaid gras. Met andere woorden: er ligt een enorme voorraad grondstof letterlijk voor het rapen! Daarenboven is het de meest duurzame grondstof die we kunnen indenken. Gras groeit acht maanden per jaar en benut hierbij de volledige oppervlakte die ter beschikking is. Dit in tegenstelling tot bomen die vele jaren nodig hebben om te groeien en op enige afstand van elkaar moeten staan. Gras neemt ook geen landbouwgrond in, behoeft geen water, kunststof mesten of pesticiden, vereist geen ontbossing en is in West-Europa in gigantische hoeveelheden beschikbaar. Kortom, geen enkele andere grondstof kan op het vlak van duurzaamheid betere troeven voorleggen.”
Florent Timmermans: “In de toekomst willen we op andere locaties productievestigingen openen omdat we het voordeel van een lokale aanvoer en distributie willen behouden."
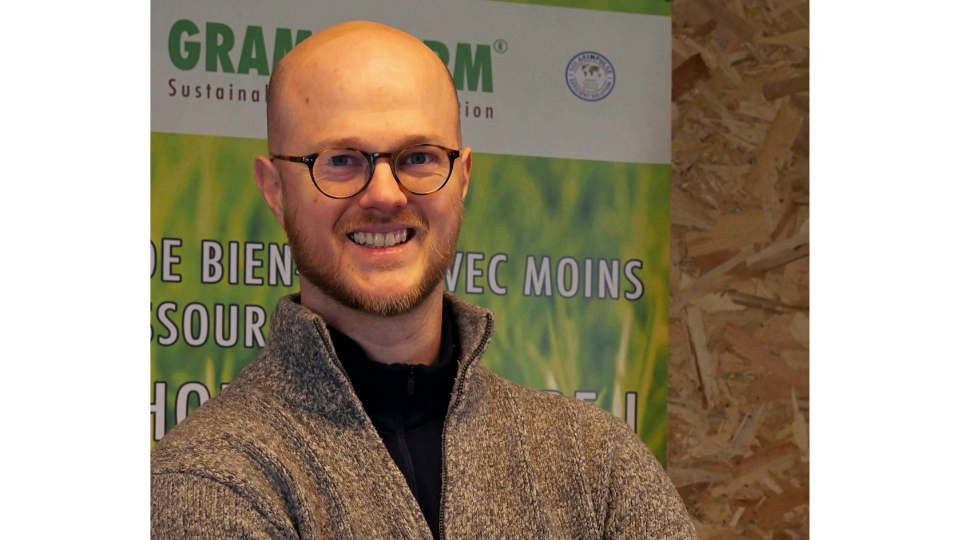
Van gras tot vezel
Het gras wordt naar de site van de biomethaaninstallatie gebracht. Meestal vers, maar in de wintermaanden wordt ‘silage-gras’ (gras dat zuurstofvrij wordt gestockeerd bij zowel de groenbedrijven als bij Gramitherm) gebruikt. “Het moet wel redelijk lang zijn omdat we vezels van 20 à 30 cm nodig hebben,” verduidelijkt Florent Timmermans. “Daarom is het interessant om met die groenbedrijven te werken, want met gras uit tuinen kunnen we niks aanvangen. Het gras wordt in Nijvel geperst, waarna de sappen – samen met andere grondstoffen – door middel van biomethanisatie in energie worden omgezet. Wat overblijft, zijn de vezels. Die worden gedurende meerdere dagen gedroogd. Hiertoe gebruiken we het warme koelingswater van de generator van de biomethanisatiefaciliteit.”
Minimaal energieverbruik
De droge grasvezel wordt in Auvelais gemengd met 20% gerecycleerde jute (afkomstig van de zakken met cacao en koffie die in de Antwerpse haven aankomen) en 10% polyester (als bindmiddel – algemeen toegepast in biobased producten). “Bedoeling is om op relatief korte termijn op volledig gerecycleerde polyester over te schakelen,” vervolgt Florent Timmermans. “Op die manier zouden we de ecologische voetafdruk nog verder kunnen minimaliseren. Helaas is er vandaag nog niet voldoende van dit materiaal op de markt beschikbaar.” Na de automatische menging worden de panelen gevormd door middel van thermoforming. Dit gebeurt in enkele minuten op een temperatuur van 160°C. “Daar maken we een enorm verschil met de productie van klassieke isolatiematerialen,” vertelt Florent Timmermans. “Het smelten van rots of glas vereist immers een temperatuur van meer dan 1300°C, en dit gedurende meerdere uren. De energie die op deze manier wordt verspild, kan in gewone gebouwen bijna niet worden gecompenseerd door de isolerende eigenschappen van het materiaal! Eigenlijk is het alleen al daarvoor de logica zelf om voor biobased isolatieplaten te kiezen…”
Christian Roggeman nam het patent over van de uitvinder Stefan Grass en zette het productieproces helemaal op punt.
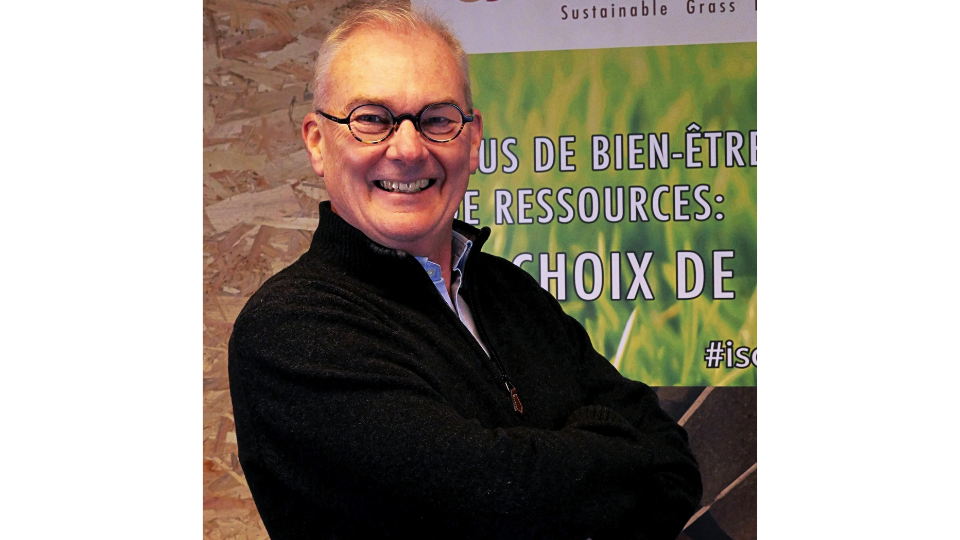
Heel wat voordelen
Natuurlijk zijn er nog andere troeven waarmee Gramitherm uitpakt om de bouwheren en aannemers voor grasgebaseerde isolatie te laten kiezen. Zoals al eerder gesteld, zou dit de meest duurzame oplossing zijn omwille van de aard van de grondstof. “Bovendien zijn de technische eigenschappen vergelijkbaar met deze van houtpanelen, vandaag het meest gebruikte biobased isolatiemateriaal,” aldus Florent Timmermans. “De isolatiewaarde tegen de koude is vergelijkbaar met deze van glas- en rotswol, en op het vlak van faseverschuiving overtreffen de graspanelen de conventionele producten. Rots- en glaswol zullen immers sneller de hitte naar binnen afgeven dan biobased alternatieven. Een enorm pluspunt is dat grasgebaseerde isolatie 100% recycleerbaar is. Zo steken wij de minder kwalitatieve stukken van het begin en einde van een batch meteen terug in de menger, en brengen de grote gebruikers hun snij-afval binnen als grondstof. Daarnaast hebben grasisolatieplaten – net als de meeste biobased materialen – geen last van uitzakking. Dat komt omdat vocht in de vezel wordt opgenomen in plaats van ertussen. Bij traditionele isolatie zien we net het omgekeerde fenomeen, wat bij vrieskou kan leiden tot uitzetting en op termijn een algemene verzakking van het materiaal. Wij garanderen dan ook een levensduur van minstens vijftig jaar, wat bij rots- en glaswol vaak utopisch is. Verder is de plaatsing van onze isolatiepanelen quasi identiek als van andere biobased materialen, weliswaar met als voordeel dat de panelen horizontaal indrukbaar zijn. Op die manier komt er minder snijwerk aan te pas. Last but not least is er de prijs… Omwille van onze alomtegenwoordige grondstof en ons uiterst energiezuinig productieproces kunnen we onze panelen zelfs goedkoper dan de meeste rotswol aanbieden!”
Het plaatsen van de Gramitherm is quasi identiek als van andere biobased materialen, met als voordeel dat de panelen ook nog eens horizontaal indrukbaar zijn.
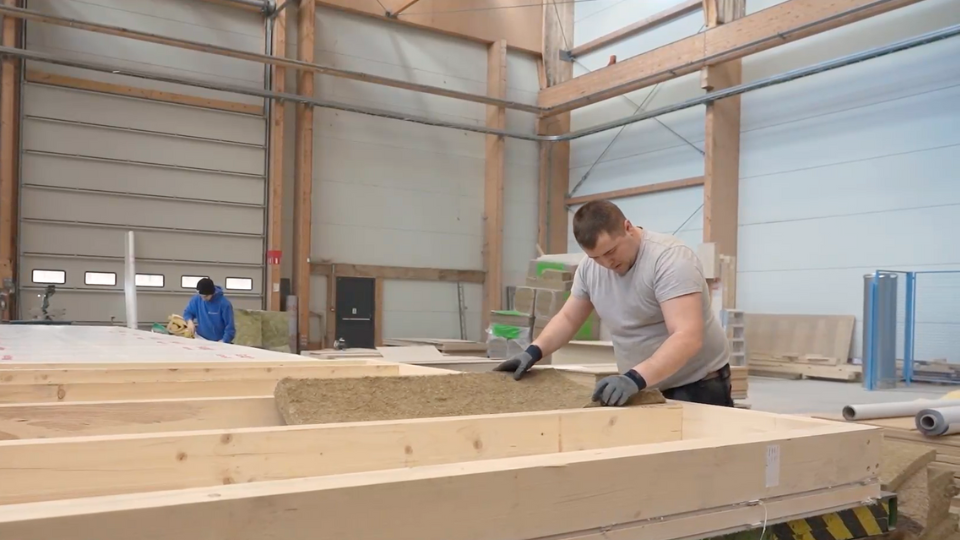
Toch een klein minpuntje
Natuurlijk is het niet allemaal goud dat blinkt. De grasisolatie valt immers nog steeds onder de Euroclass E qua brandbeveiliging. “Dit is een barrière waartegen vele producenten van biobased materialen aanbotsen”, vertelt Florent Timmermans. “Helaas is de reglementering nog niet op duurzaam/circulair bouwen afgestemd. Bij de testen wordt vandaag gekeken of het oppervlak afbrandt wanneer er een vlam voor wordt gehouden. Door de specifieke aard van grasvezel is dat effectief het geval, maar dat betekent geenszins dat ons product minder brandveilig is. Integendeel, door toepassing van een brandvertrager op basis van mineraalzout stopt de verspreiding van het vuur vanaf het moment dat de vlam wordt weggehaald. Waarmee in de regelgeving geen rekening wordt gehouden, is dat polyurethaan bij brand steevast een zwarte toxische rook zullen afgeven, terwijl dat bij onze graspanelen – dankzij de natuurlijke eigenschappen van gras en jute – een witte, volatiele rook zal zijn. En waar sterven de meeste mensen aan in een brand? Juist… verstikking door de toxische rook.”
Razendsnelle groei
De Euroclass E blijkt Gramitherm niet in haar opmars te stuiten. “Onze isolatieplaten kunnen perfect in woon- en kantoorcomplexen tot zeven verdiepingen worden toegepast”, aldus Florent Timmermans. “Hogere gebouwen mogen wettelijk gezien niet met een E-isolatie worden uitgerust, maar voor alle andere toepassingen is het zeker interessant om voor de grasplaten te kiezen. En we zien dat er wel degelijk een grote interesse bestaat. In 2023 produceerden we 15.000 m³ panelen die via verdelers en groothandelaars in België, Nederland, Frankrijk, Luxemburg en een klein beetje Italië in de markt werden gezet. De meeste exemplaren werden trouwens door professionele installateurs gebruikt. Op erg korte termijn groeide de vraag enorm, met als gevolg dat we onze capaciteit tegen eind dit jaar zullen moeten verdubbelen. In de toekomst willen we op andere locaties productievestigingen openen omdat we het voordeel van een lokale aanvoer en distributie willen behouden. Frankrijk staat al op de radar, maar we dromen natuurlijk nog verder… tot in Noord-Amerika. Eigenlijk is het een half wonder dat we staan waar we nu staan. Net toen we met de productie wilden starten, sloeg de pandemie toe, wat ons tot op de rand van de afgrond bracht. Gelukkig geloofden we zo sterk in Gramitherm dat we er met man en macht voor zijn blijven strijden. En dat heeft ons geen windeieren opgebracht, want de business floreert sterker dan we ooit hadden durven hopen. In die mate dat we nu al negentien fulltime medewerkers in dienst hebben en tegen eind dit jaar een positieve ebidta zullen kunnen voorleggen.”