Unicum in België: Soprema maakt bitumen circulair
Heel wat actoren in de Belgische bouwsector geloven sterk dat circulariteit het enige pad is dat naar een succesvolle toekomst leidt. Ook Soprema onderschrijft deze visie, en niet alleen met woorden, maar ook met concrete daden. Na een indrukwekkende piloot voor de upcycling van EPS in Tongeren bouwt de Franse gigant nu een fabriek in Grobbendonk waar snijresten van roofing in een volwaardige grondstof voor bitumen zullen worden omgezet. Hiermee schrijft ons land een wereldprimeur op haar naam, want het is voor de eerste keer dat dit gepatenteerde proces op industriële schaal gebeurt.
Het project omvat ook nog de verdubbeling van de bestaande productieruimte en de bouw van nieuwe magazijnen en kantoren.
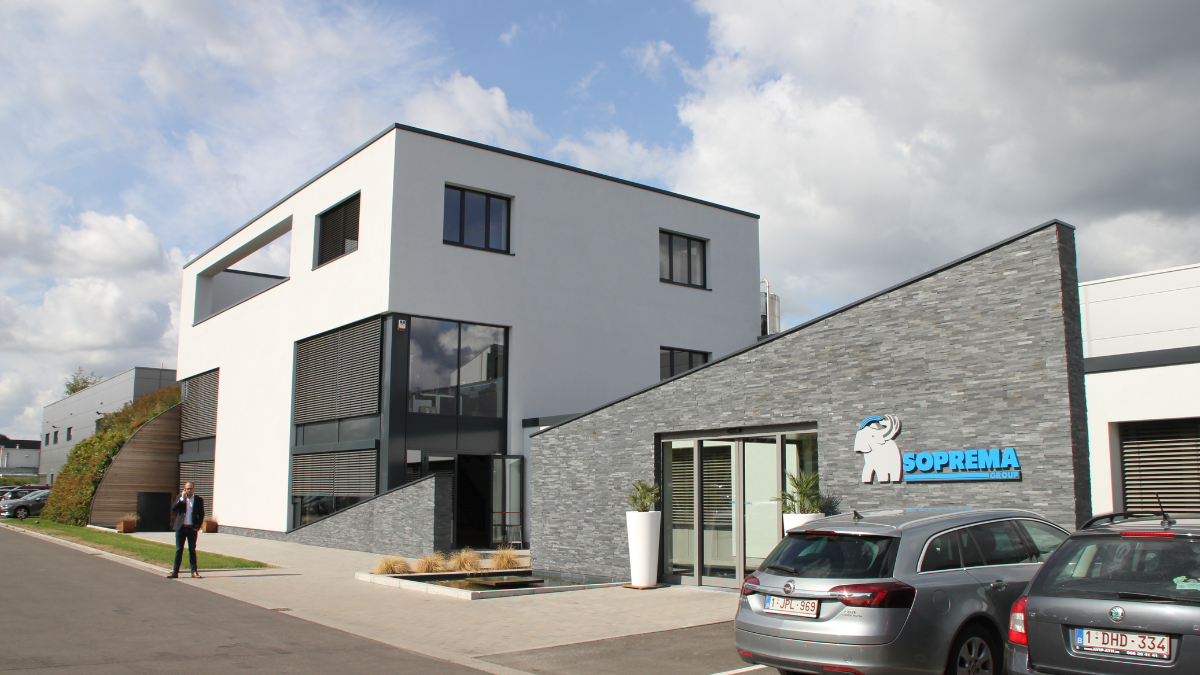
Met 115 jaar op de teller is Soprema een merk dat zichzelf intussen al miljoenen keer heeft bewezen. Het Franse familiebedrijf baande zich met kwaliteit en innovatief vermogen een weg naar de mondiale top in het domein van dakbedekking, waterdichting en isolatie. Enkele cijfers die dit illustreren: 5 miljard euro omzet, bijna 12000 werknemers wereldwijd, actief in 90 landen, 123 productiesites, 23 R&D-centra, meer dan 120 dochterondernemingen… In dit plaatje neemt België een sleutelpositie in. Hans Van Glabeke, marketingmanager Soprema Belux, legt uit: “Niet alleen telt ons land drie fabrieken, 250 werknemers en het R&D-centrum bitumen voor Noord-Europa. Ook openden we enkele jaren geleden in Tongeren een unieke recyclagefabriek waar piepschuim – ingezameld bij onder meer Fnac Vanden Borre en de Vismijn van Oostende - voor 100% wordt omgezet in grondstof die we op dezelfde site tot XPS-isolatie verwerken. Vandaag bereiken we een nieuwe mijlpaal: de productiesite voor bitumen in Grobbendonk werd door de grep immers uitgekozen als locatie voor de ZLOOP, een fabriek waarmee voor de eerste keer op industrieel niveau bitumineus snij- en sloopafval maximaal in nieuwe hoogwaardige bitumen dakbedekking wordt omgezet.”
De bedoeling is om met de ZLOOP tegen eind 2024 meer dan 6000 ton recyclaat te maken.
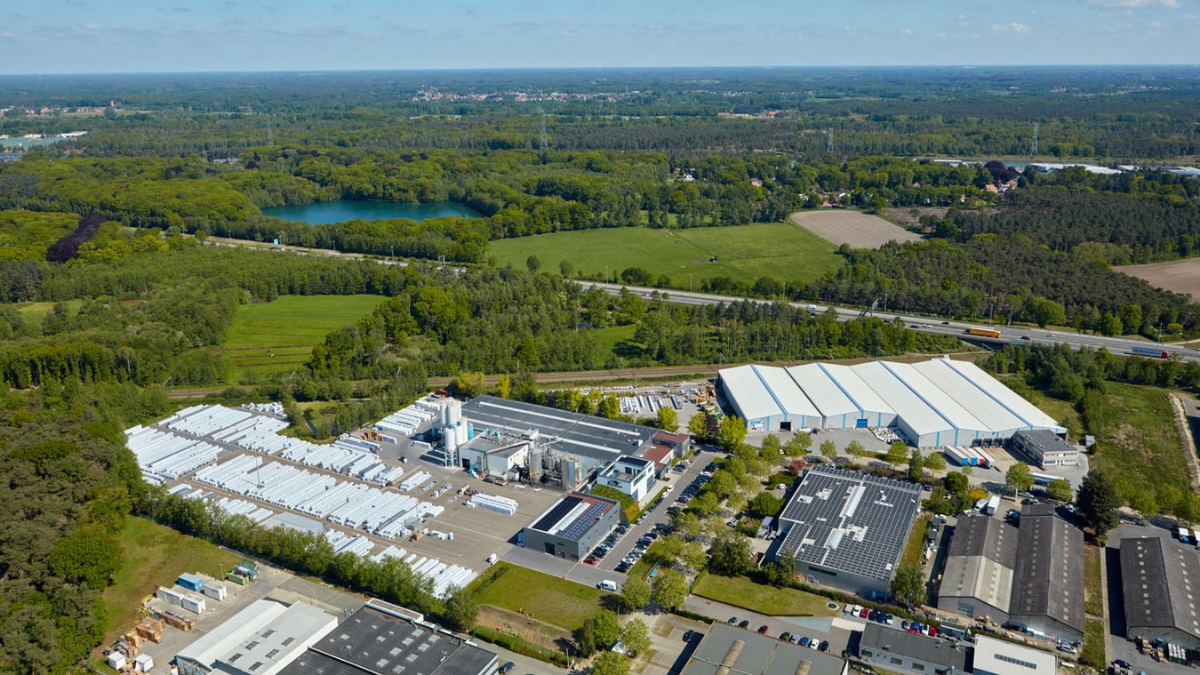
Ecologische voetafdruk reduceren
Aan het project hangt een prijskaartje van dertig miljoen euro, waarvan het innovatieve deel voor 30% wordt meegefinancierd door de Europese Unie via het RRF in het kader van het ‘Vlaams veerkacht’-project. Deze investering maakt deel uit van Soprema’s ambitie om de bouwsector te verduurzamen en zelf tegen 2030 CO2-neutraal te werken. “Ik ben er bijzonder fier op dat we oplossingen produceren die een essentieel onderdeel zijn van de strijd tegen de opwarming van de aarde”, stelt managing director Belux, Marc Geerts. “Enerzijds is er onze XPS-isolatie die volgens ons dé norm in de toekomst zal worden (zie kaderstuk - nvdr). Anderzijds produceren we dakoplossingen die regenwater opvangen, zonne-energie produceren, dienst doen als recreatieruimte, een stukje groen in stedelijke omgevingen brengen… Weliswaar zijn deze systemen pas écht duurzaam indien ze een minimale ecologische voetafdruk hebben. Om dit te realiseren, komen we al snel bij de term ‘circulariteit’ uit. Recyclage volstaat niet om het probleem van afval en schaarse grondstoffen op te lossen. In onze sector zijn er genoeg initiatieven om bitumenrestanten te recycleren, maar dat zijn ‘downsizing’-projecten die resulteren in minderwaardige grondstoffen voor onder meer de wegenbouw. Wij wilden beter doen door het roofing-afval te verwerken tot een hoogwaardige grondstof waarmee opnieuw kwaliteitsvolle bitumen kunnen worden gefabriceerd. Aanvankelijk spreken we over snijresten, maar op termijn willen we het proces natuurlijk ook op sloopafval toepassen.”
Complexiteit troef
Het concept van de ZLOOP werd uitgedokterd door het internationale R&D-team van Soprema. In 2020 werd een prototype (de XLOOP) op de site in Val-de-Reuil in Frankrijk gebouwd. “De realisatie van deze innovatie was een werk van lange adem,” aldus plant manager Tom Vloemans. “Vooral de grote variëteit aan bitumen op de Europese markt was een moeilijk te nemen hindernis. Ons eigen gamma telt al meer dan honderd varianten, en daarnaast wilden we ook het aanbod van de concullega’s kunnen verwerken. Daarom moesten we een systeem ontwikkelen dat alle componenten van zo’n dak - bitumen, vulstoffen, polyester, steentjes, folies… - van elkaar kan scheiden. Bovendien moest het recyclageproces zowel op plastomeren als elastomeren kunnen worden toegepast, de twee types bitumen die in ons land circuleren.”
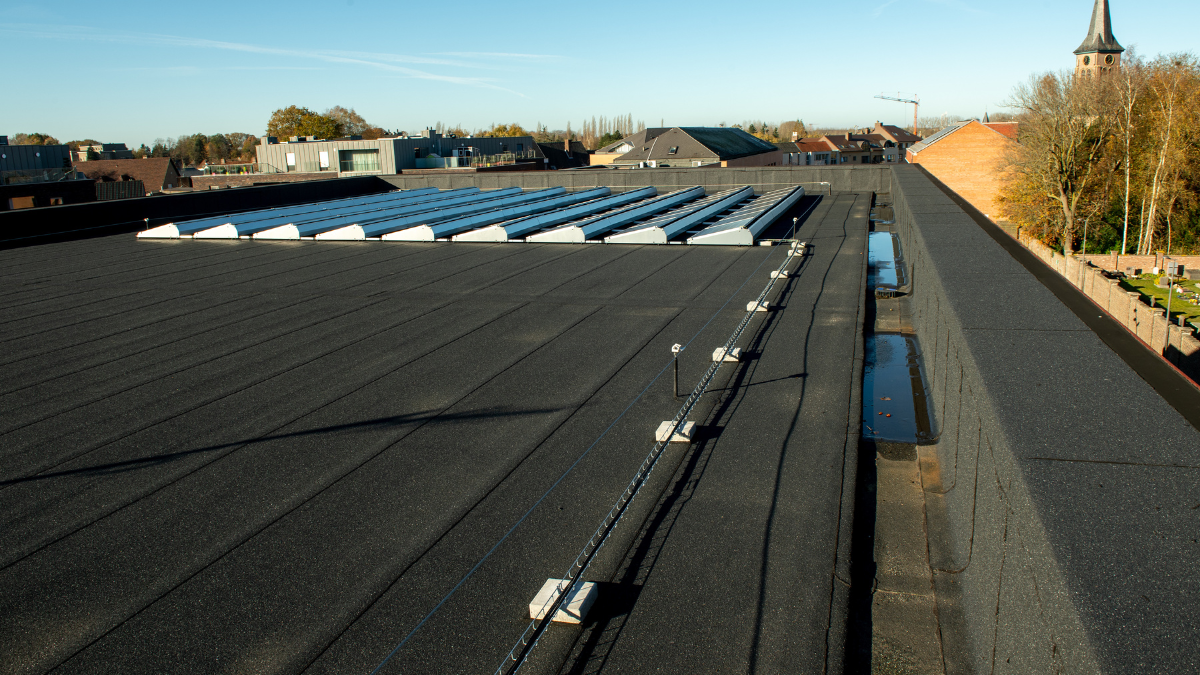
Missie geslaagd
Toch kregen de ingenieurs van de Soprema Group het onmogelijke voor elkaar. “Met de XLOOP werd in 2021 zo’n 300 ton snij-afval in grondstof voor nieuwe hoogwaardige bitumen omgezet”, vertelt Marc Geerts. “Natuurlijk ligt het recyclagepotentieel vele keren hoger. Daarom beoogde de groep een opschaling op industrieel niveau. Ons R&D-team stond opnieuw voor een ambitieuze opdracht, want een dergelijke recyclagefabriek bestaat nergens ter wereld. Niettemin slaagden de ingenieurs ook in deze missie: vandaag bouwen meerdere machineproducenten op basis van hun ontwerpen een compleet productieapparaat dat over enkele maanden in het nieuwe fabrieksgedeelte in Grobbendonk zal worden geïmplementeerd.”
Aanvoer afval in testfase
De ZLOOP wordt door Edibo gebouwd achter de bestaande bitumenfabriek van Soprema in Grobbendonk. “Concreet komt er een hal in staalstructuur van ongeveer 4000 m²,” aldus Marc Geerts. “De bedoeling is om tegen eind 2024 meer dan 6000 ton recyclaat te maken. Dit is genoeg grondstof om zo’n twee miljoen m² dak waterdicht te maken. Weliswaar is dat maar een fractie van onze productie: alleen al in Grobbendonk fabriceren we jaarlijks bitumen voor zo’n 12 miljoen m² dakbedekking. Toch is dit project geen druppel op een hete plaat. Integendeel, er hangt een reëel businessmodel aan de investering en we rekenen op een terugverdientijd van minder dan tien jaar. Bovendien is er de mogelijkheid om zonder veel extra centen de recyclagecapaciteit met een factor drie op te trekken. In een eerste fase willen we zuiver snij- en productieafval van bitumen verwerken. Hiertoe hebben we samen met de federatie ProBitumen het ‘Bitumen Recycling Network’ opgezet. In dit kader worden binnenkort big bags uitgedeeld aan dakdekkers. Bedoeling is uit te testen op welke manier en door welke partijen dit afval het best wordt gecollectioneerd, welk prijskaartje aan deze logistieke operatie hangt… We gaan ervan uit dat de dakwerkers dit nieuwe concept zullen omarmen, want ze hebben er alleen maar bij te winnen. Vandaag moeten ze immers alle snij-afval nog naar een containerpark brengen.”
De bedoeling is om tegen eind 2024 meer dan 6000 ton recyclaat te maken.
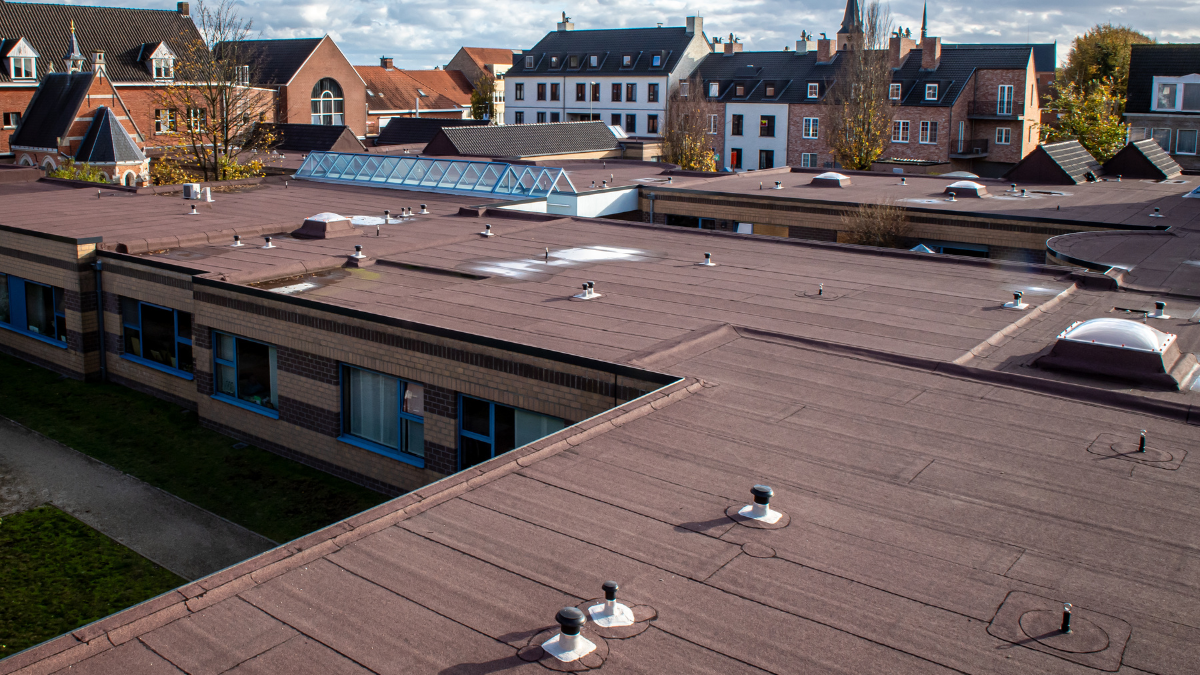
24-7 productie
Over het effectieve recyclageproces willen de gesprekspartners weinig kwijt. Begrijpelijk, want het proces is grotendeels gepatenteerd. Samengevat bestaat de eerste fase uit het shredderen van het afval. Tom Vloemans: “Door middel van een mechanische bewerking worden alle bitumen gereduceerd tot stukken van ongeveer 10 cm². Deze worden daarna gescreend op metalen en andere vervuilingen. Vervolgens zijn er een resem thermische en mechanische bewerkingen met filters en speciale toestellen. Het resultaat is een vloeibare massa van bitumen die we in opslagtanks opslaan om uiteindelijk in de productie aan te wenden.” Soprema heeft de intentie om de fabriek 24-7 te laten draaien, wat de tewerkstelling in de regio ten goede komt. Per shift zijn immers een vijftal extra werkkrachten nodig. Indien alles volgens plan verloopt, zou de opstart in het derde kwartaal van 2024 gebeuren. Het project omvat trouwens ook nog de verdubbeling van de bestaande productieruimte en de bouw van nieuwe magazijnen en kantoren. Een interessant weetje: Soprema zal op deze werf voor de eerste keer ooit losse isolatie aanleveren die in geprefabriceerde betonpanelen kan worden ingestort. Ook dit is een primeur die wel eens voor enige beweging in de sector zou kunnen zorgen…
Nadenken over circulariteit
Zoals al eerder aangegeven, wil Soprema in de toekomst graag ook sloopafval verwerken, maar uit reeds uitgevoerde testen blijkt dat er nog werk aan de winkel is om dit een realiteit te maken. Vooral de chemische bevestiging is een breekpunt, want hierdoor bevat het sloopafval heel wat vervuiling (stukjes hout, steen, beton…). “Circulariteit wordt het kernbegrip van de toekomst”, aldus Marc Geerts. “Als producent hebben we de morele plicht om onze oplossingen daarop af te stemmen. Zo zetten wij nu al in op de ontwikkeling van membranen die gemakkelijker te recycleren vallen en mechanisch kunnen worden bevestigd. We beschikken zelfs over een team van tien medewerkers die bouwheren, architecten en aannemers bijstaat om al in de conceptuele fase de meest circulaire oplossing voor dakbedekking/dichting en isolatie uit te dokteren. Ervoor zorgen dat producten herbruikbaar zijn, is essentieel om een duurzame bouwsector te realiseren. Eerst hergebruik, dan recyclage. De impact van een product dat je telkens opnieuw kunt gebruiken is veel groter dan de impact van hernieuwbaar of recycleerbaar materiaal dat niet circulair is.”
Soprema zet nu al in op de ontwikkeling van membranen die gemakkelijker te recycleren vallen en mechanisch kunnen worden bevestigd.
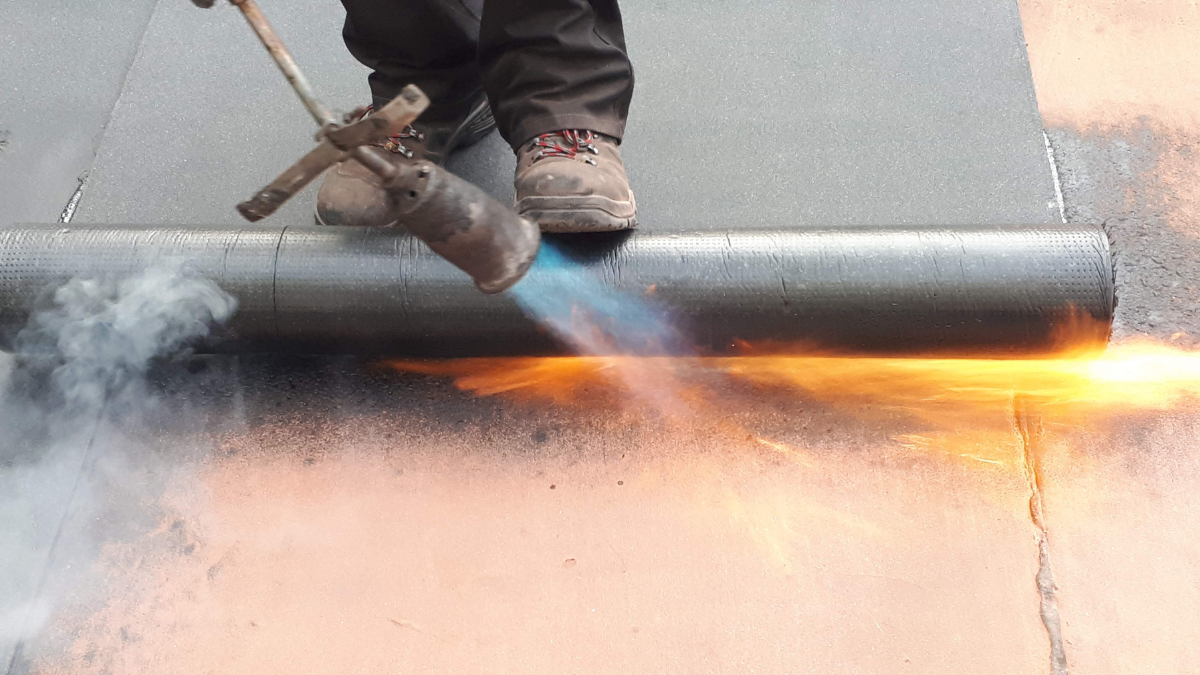
XPS-isolatie
Een paradepaardje van Soprema is de isolatiefabriek in Tongeren-Oost, en dit niet alleen omwille van het unieke recyclageproces van EPS. In deze productiefaciliteit wordt ook een product gemaakt waar de firma bijzonder trots op is: XPS-platen (geëxtrudeerd polystyreen). “Dit isolatiemateriaal is erg breed inzetbaar: van (funderings)muren en gevels, over vloeren en daken, tot parkings en parkeerdaken”, aldus Hans Van Glabbeke. “Zelfs voor omkeerdaken is XPS een volkomen veilige keuze. Het grote voordeel is de gesloten celstructuur waardoor deze isolatie vochtwerend en bestand tegen schimmels is. Daarnaast kan het van gerecycleerde EPS worden gemaakt én is het op zijn beurt recycleerbaar. Gecombineerd met de hoge druksterkte, lange levensduur en gemakkelijke verwerkbaarheid is dit volgens ons dé isolatieoplossing voor circulaire bouwprojecten.”
XPS-platen zijn erg breed inzetbaar, kunnen van gerecycleerde EPS worden gemaakt en zijn op hun beurt recycleerbaar.
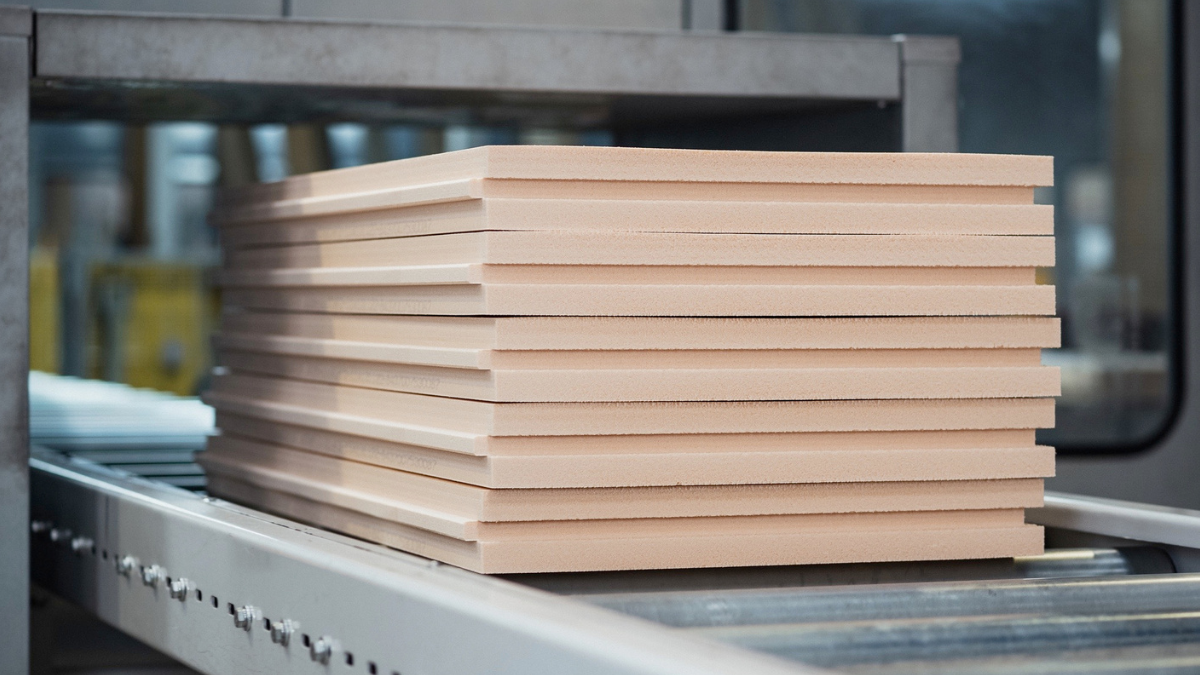