Residentie Victory: katalysator voor innovaties bij specialist in architectonisch prefabbeton
Op wandelafstand van het Woluwe Shopping Center zag in juli vorig jaar Residentie Victory het levenslicht. Het project omvatte de reconversie van een kantorengebouw in 97 woongelegenheden, gaande van studio’s tot appartementen met 3 slaapkamers.
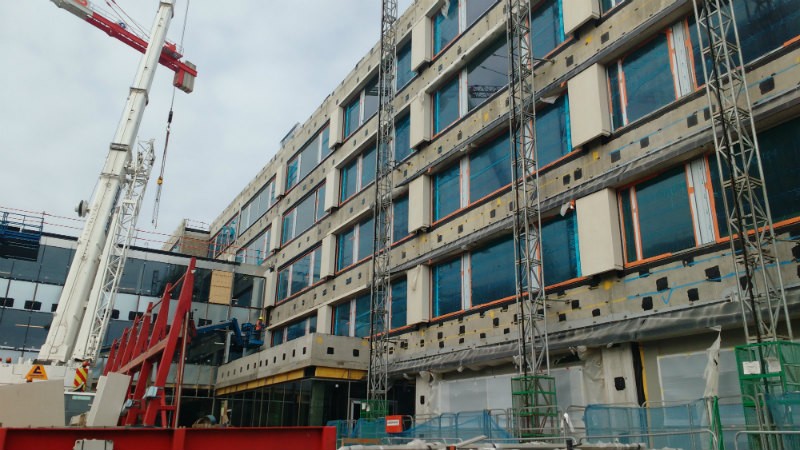
Verheyen Beton, dat instond voor de terrassen, besliste kort na - en deels door die klus - om voortaan ook voorgespannen betonelementen te gaan produceren. “In tegenstelling tot bij traditioneel gewapend beton, komt bij voorgespannen beton scheurvorming of doorbuiging veel minder vaak voor,” klinkt het.
Residentie Victory, dat naast appartementen ook bestaat uit een ondergrondse garage met 100 plaatsen, werd ontworpen door DDS & Partners Architects, voor vastgoedontwikkelaar Immogra. Verheyen Beton uit Arendonk, dat werk biedt aan zo’n 80 werknemers, is specialist in architectonisch prefabbeton en stond in voor de studie en productie van de 75 terraselementen en alle verankeringsonderdelen ervan. De terrassen werden in uitkraging uitgevoerd in antractiet gezuurd beton.
Michel Catteau, Algemeen Directeur bij Verheyen: “Normaliter worden de terraselementen tijdens de opbouw van de structuur mee aangestort aan de vloerplaat. In dit geval hebben we een verankering moeten uitwerken, zodat de terrassen mechanisch, vanuit een kraan, gemonteerd konden worden. Er was dus geen ondersteuning nodig, en ook geen opstort van beton of andere natte knopen. Er werden twee verankeringen voorzien per balkon. De vormgeving van de terrassen was een andere uitdaging. De elementen moesten immers zeer slank zijn. Een traditionele wapening was daardoor niet mogelijk. Daarom hebben wij voorgesteld om die elementen na te spannen. Zodoende kon men de sectie van de elementen behouden en de doorbuiging tot een minimum herleiden,” aldus Michel Catteau.
Voorspantafels
Verheyen heeft de keuze gemaakt om te investeren in de installatie van voorspantafels, om voortaan ook voorgespannen beton te kunnen produceren. “We kwamen in dit project nogmaals tot de vaststelling dat voorgespannen betonelementen gewoon heel veel voordelen hebben ten opzichte van traditioneel gewapend beton. Doorbuiging en vooral scheurvorming kunnen gedeeltelijk of in sommige gevallen zelfs volledig vermeden worden.” zegt Catteau.
Mechanische koppeling van balkons aan een bestaande structuur
Een tweede recente innovatie van Verheyen is een mechanisch verankeringssysteem voor uitkragende betonelementen. Het bedrijf ontwikkelde dit samen met zusterfirma Hooyberghs uit de B&R bouwgroep.
Michel Catteau verduidelijkt waar deze innovatie voor staat: “Dit systeem is gebaseerd op de ervaringen die we opdeden tijdens het Victory project en ook op de vraag van onze klanten. Het systeem heeft enkele grote voordelen. Er is geen onderstempeling nodig, want de montage gebeurt rechtstreeks vanuit de kraan. De montage kan gebeuren na het optrekken van de structuur en het afwerken van de gevel, wat vervuiling van de terrassen tijdens de werken bijna volledig uitsluit. Tot slot gebeurt de montage binnen in het gebouw, wat de veiligheid ten goede komt.
Ondertussen is het systeem gepatenteerd en zijn er verregaande gesprekken met een gespecialiseerde firma in verankeringstechnieken, voor de verdere commercialisatie. Eind dit jaar zal dit systeem op de markt komen.”
Buitenlandse activiteiten
Het toepassen van voorspanning in architectonisch beton werd vorig jaar al in de praktijk gebracht voor het nieuwe kantoorgebouw van Cambridge Assessment in Cambridge, in het Verenigd Koninkrijk – meteen ook de eerste buitenlandse activiteit van Verheyen Beton. De 405 lintelen die het metselwerk van dit gebouw moesten dragen, dienden een typische lengte te hebben van 9 meter. Gezien de kleine sectie van 30 cm breed op 15 cm hoog, was het quasi onmogelijk om de elementen in klassiek gewapende uitvoering in ongescheurde toestand te transporteren en te manipuleren. Daarom werden de elementen voorgespannen.
Prefabricage van architectonische gevelelementen
In september 2015 begonnen de werken voor het nieuwe kantoorgebouw van Cambridge Assessment in Cambridge (VK). Het nieuwe gebouw, gelegen aan de Shaftesburry road, wordt The Triangle Project genoemd en zal tegen 2025 plaats bieden aan drieduizend werknemers.
Het ontwerp werd getekend door Eric Parry Architects en HLM Architects werd als uitvoerend architect aangesteld. Aannemer Bouygues-UK neemt de uitvoering en afwerking voor zijn rekening. De oplevering van het gebouw is voorzien voor september 2017. Eind 2015 werd de prefabricatie van de architectonische gevelelementen toegewezen aan Verheyen Beton uit België. Deze relatief late toewijzing vroeg extra inspanningen van de engineering-afdeling, om alles tijdig uit te werken. De grootste troeven die Verheyen Beton uitspeelde om dit project binnen te halen, waren de kwaliteit, het voorspannen van de lange smalle lintelen en het combineren van diverse kolommen en balken tot portiekelementen.
De 405 lintelen die het metselwerk dragen, dienden een typische lengte te hebben van 9 meter. Gezien de kleine sectie (30 cm breed en 15 cm hoog) was het quasi onmogelijk om de elementen in klassiek gewapende uitvoering in ongescheurde toestand te transporteren en te manipuleren. Om scheurvorming te vermijden, werden de elementen voorgespannen. Bijkomende moeilijkheid was de grote spouwbreedte van 36 cm, hierdoor was de verankering van deze lintelen geen evidentie. Ter hoogte van de voegen werden 624 opgehangen gevelpanelen voorzien.
De montage van de 1.029 gevelelementen gebeurde rechtstreeks van de vrachtwagen door drie installatieploegen. Op piekmomenten stonden gelijktijdig meer dan twaalf opleggers van de transporteur op de reeds drukbevolkte werf geparkeerd. Aan de courtyards werd in het ontwerp een zonnewering voorzien bestaande uit 912 gestapelde balken en kolommen. Dit werd door Verheyen Beton omgezet naar gecombineerde portieken. Hierdoor werden maar liefst 712 kraanbewegingen uitgespaard, wat de hogere kost van de elementen op zich meer dan verantwoordde. De montage van de 160 brise-soleil-elementen gebeurde door een afzonderlijk team en een 350-tons kraan. Op piekmomenten werden er tot acht elementen per dag gemonteerd, waardoor er een gegarandeerde aanvoer moest zijn van vier vrachten per dag.